Ball joints in reciprocating engine exhaust systems should be – Ball joints play a crucial role in reciprocating engine exhaust systems, ensuring efficient and reliable operation. Their function and design are paramount to the overall performance and longevity of these systems.
This comprehensive guide delves into the intricacies of ball joints, exploring their types, design considerations, manufacturing processes, installation and maintenance procedures, troubleshooting techniques, and successful case studies. By gaining a thorough understanding of these aspects, engineers and technicians can optimize the performance of reciprocating engine exhaust systems, ensuring maximum efficiency and extended service life.
Ball Joints in Reciprocating Engine Exhaust Systems: Ball Joints In Reciprocating Engine Exhaust Systems Should Be
Ball joints play a crucial role in reciprocating engine exhaust systems, ensuring efficient and reliable operation. These joints connect the exhaust manifold to the exhaust pipe, allowing for flexibility and movement as the engine vibrates and expands.
Types of Ball Joints, Ball joints in reciprocating engine exhaust systems should be
- Spherical Ball Joints:Offer a wide range of motion and are suitable for high-temperature applications.
- Pivot Ball Joints:Provide a limited range of motion and are often used in systems with space constraints.
- Universal Ball Joints:Combine the advantages of spherical and pivot ball joints, providing flexibility in multiple directions.
Design Considerations
The design of ball joints for reciprocating engine exhaust systems must consider several factors:
- Temperature:Exhaust gases can reach high temperatures, requiring ball joints to withstand extreme heat.
- Vibration:The engine’s vibrations can cause stress on the ball joints, affecting their longevity.
- Corrosion:Exposure to exhaust gases and moisture can lead to corrosion, compromising the integrity of the joints.
- Material Selection:Ball joints are typically made from high-temperature alloys or stainless steel to ensure durability and corrosion resistance.
FAQ Section
What are the different types of ball joints used in reciprocating engine exhaust systems?
There are two main types: spherical ball joints and self-aligning ball joints. Spherical ball joints offer a wide range of motion, while self-aligning ball joints compensate for misalignment and reduce stress on the joint.
What are the key design considerations for ball joints in reciprocating engine exhaust systems?
Factors such as load capacity, temperature resistance, corrosion resistance, and wear resistance are crucial. The design must also accommodate the system’s vibrations and thermal expansion.
How are ball joints manufactured for reciprocating engine exhaust systems?
Precision machining, heat treatment, and surface coating processes are employed to ensure durability and longevity. Quality control measures include dimensional inspections, material testing, and performance evaluations.
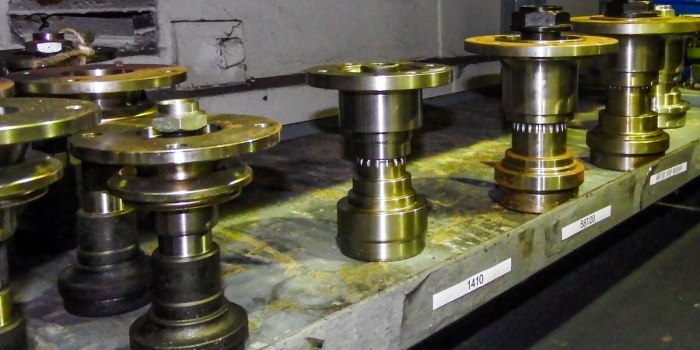
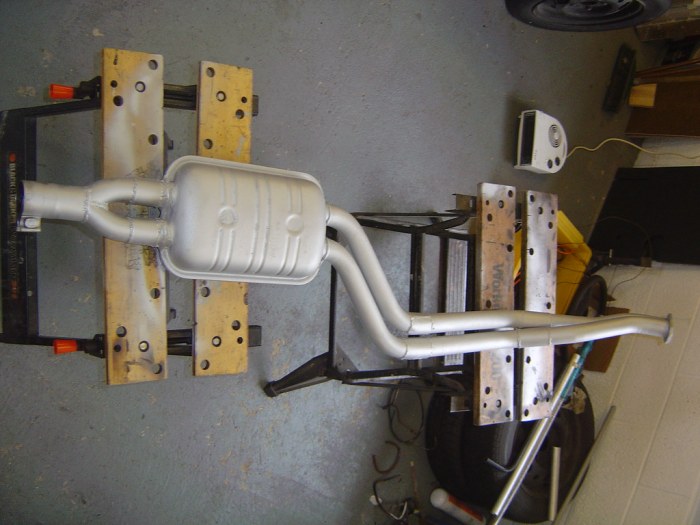
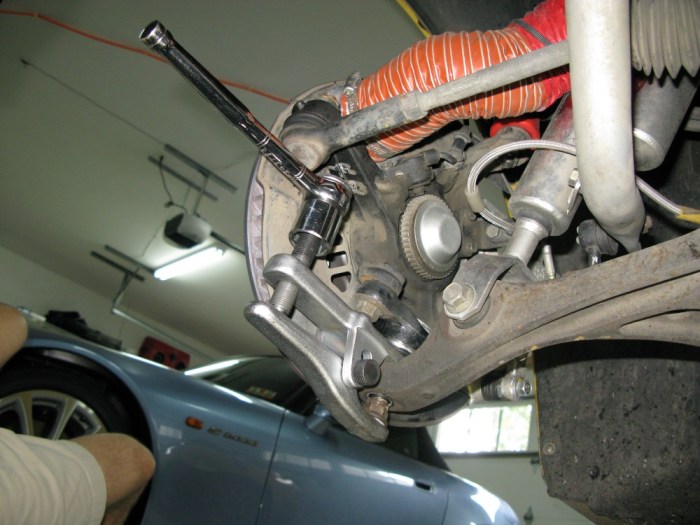